
Challenge
L'usine d'ammoniac Nutrien de Borger, au Texas, rencontrait régulièrement des défaillances de tubes dans ses chaudières à récupération de chaleur. Une moyenne de deux pannes par an des générateurs de vapeur représentait un impact financier important en termes de maintenance et de perte de production, puisque chaque arrêt coûtait environ [#0]} [#1]} $ en réparations, sans compter les pertes de production.
L'usine d'ammoniac de Kellogg, d'une capacité de 1500 tonnes par jour (TPD), a besoin de vapeur à 1500 psig pour faire fonctionner les turbines et les compresseurs, ainsi que pour chauffer les différentes étapes du processus. Le système génère 520 klb/h de vapeur à partir d'une eau d'alimentation de grande pureté qui est traitée à l'aide d'un programme coordonné de pHphosphate (également appelé phosphate congruent). Le contrôle du traitement est essentiel pour prévenir les risques de corrosion caustique et acide dans les zones à flux thermique élevé des chaudières.
Un programme coordonné de pH-phosphate utilise deux mélanges de produits phosphate-caustique pour contrôler le pH de l'eau de la chaudière qui est susceptible de fluctuer en raison de la présence d'impuretés, telles que le chlorure ou le sulfate. Les opérateurs de la centrale à vapeur testent fréquemment le pH et le phosphate de l'eau de la chaudière, ainsi que d'autres indicateurs de contrôle. Les résultats sont enregistrés dans InSight*, le système de gestion des données de Veolia basé sur le cloud, qui utilise des analyses brevetées pour orienter les opérateurs dans l'ajustement de l'application du traitement.
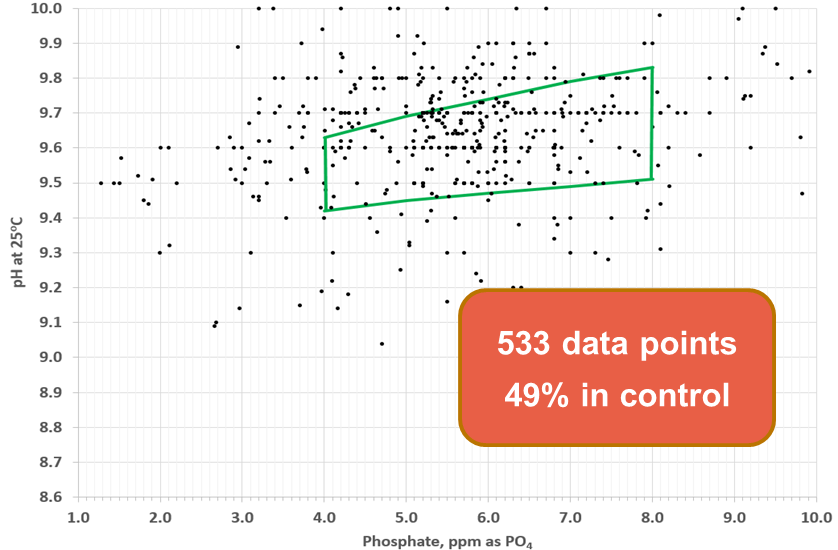
En raison de la variabilité de la qualité de l'eau d'alimentation ainsi que du fait que l'application et le contrôle du traitement étaient effectués manuellement, le pH et le phosphate de l'eau de chaudière évoluaient constamment à l'intérieur et à l'extérieur des limites autorisées. En fonctionnement normal, plus de 50 % des mesures se situaient en dehors des limites fixées (figure 1), pouvant ainsi expliquer les défaillances récurrentes des tubes de la chaudière. Nutrien Borger souhaitait améliorer le contrôle du pH et du phosphate de l'eau de la chaudière afin de réduire les coûts associés aux pannes de celle-ci.
Solution
Veolia a recommandé d'utiliser un système automatisé pour surveiller les paramètres de l'eau et de le relier directement à l'application de traitement en continu. Le Boiler Precision System (BPS) utilise les relevés d'une sonde pH en ligne pour déterminer le mélange adéquat de produits phosphatés à appliquer en temps réel (Figure 2). Le dosage des produits chimiques est contrôlé par un signal de débit de vapeur provenant du système de commande numérique de l'usine, de manière à ce que les taux de dosage soient proportionnels à la production de vapeur. Il est possible d'améliorer encore le contrôle en ajoutant un débitmètre de purge et en associant le débit d'alimentation en produits chimiques à cette lecture. Cela permettrait d'optimiser le contrôle de ce qui est alimenté et de ce qui est évacué de la chaudière. L'usine de Borger envisage de mettre en œuvre ce système à l'avenir.
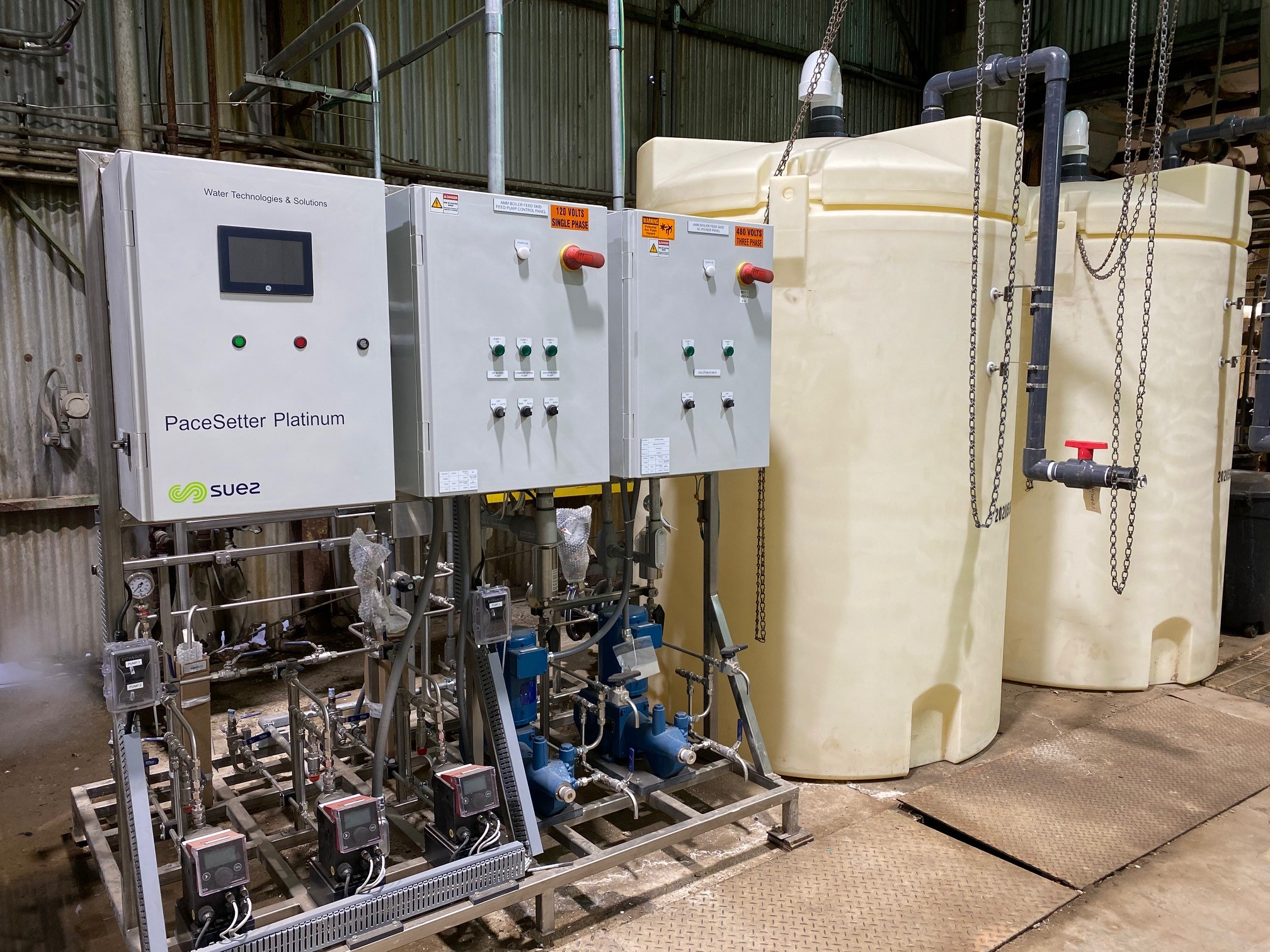
L'utilisation d'un système automatisé de contrôle et de dosage des produits chimiques garantit que les tests et les ajustements sont effectués en continu, au lieu de quelques fois par jour, comme c'est le cas lorsque les opérateurs effectuent des tests de laboratoire et ajustent le traitement manuellement.
Résultat
Dès que le système BPS a été opérationnel, le pH et le phosphate de l'eau de la chaudière se sont stabilisés. En quelques jours, nous avons pu constater que le système permettait une nette amélioration du contrôle du traitement, avec plus de 80 % des valeurs dans la plage de contrôle (figure 3).
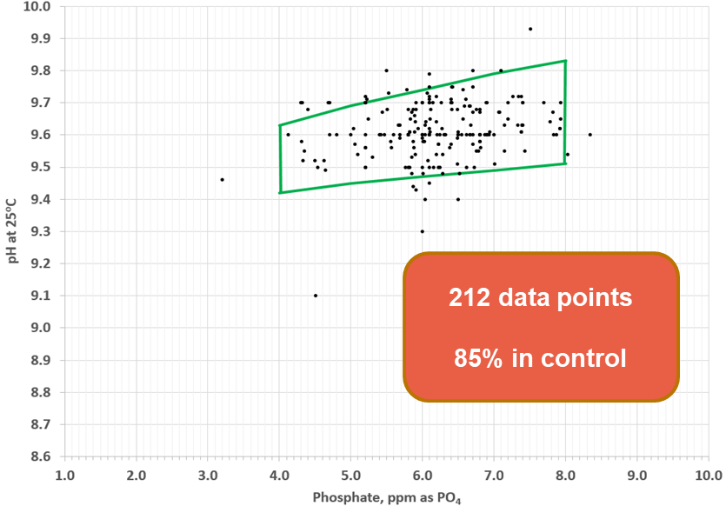
Au-delà de la lecture en continu et de l'ajustement chimique, le système BPS intègre également une unité de contrôle de la température de l'échantillon, qui garantit que la mesure du pH est effectuée dans des conditions maîtrisées, réduisant de ce fait la marge d'erreur.
La mise en œuvre du système BPS avec dosage automatique des produits chimiques a réduit le risque de sécurité lié à l'exposition aux produits chimiques, puisque les opérateurs n'ont pas à travailler aussi fréquemment à proximité des pompes et des réservoirs d'alimentation en produits chimiques. Bien que les opérateurs doivent toujours effectuer des tests à chaque poste pour valider les relevés en ligne, le temps précédemment consacré à la préparation des lots de produits chimiques peut être alloué à d'autres tâches à valeur ajoutée.
« Depuis que Veolia nous fournit ses services de traitement de l'eau et son expertise, notre partenariat a permis d'apporter de nombreuses améliorations à nos installations. Le Boiler Precision System a amélioré la fiabilité de la chaudière, la fiabilité de l'application des produits chimiques et a considérablement réduit les temps d'arrêt imprévus ».
Mark Marquez, superviseur de l'ammoniac chez Nutrien à Borger
Au cours des 12 mois qui ont suivi l'installation du BPS, il n'y a pas eu une seule défaillance de tube de la chaudière à l'usine de Nutrien à Borger. La réduction des coûts de maintenance et l'amélioration de la durée de vie des installations ont été estimées à 275 000 $ par an.