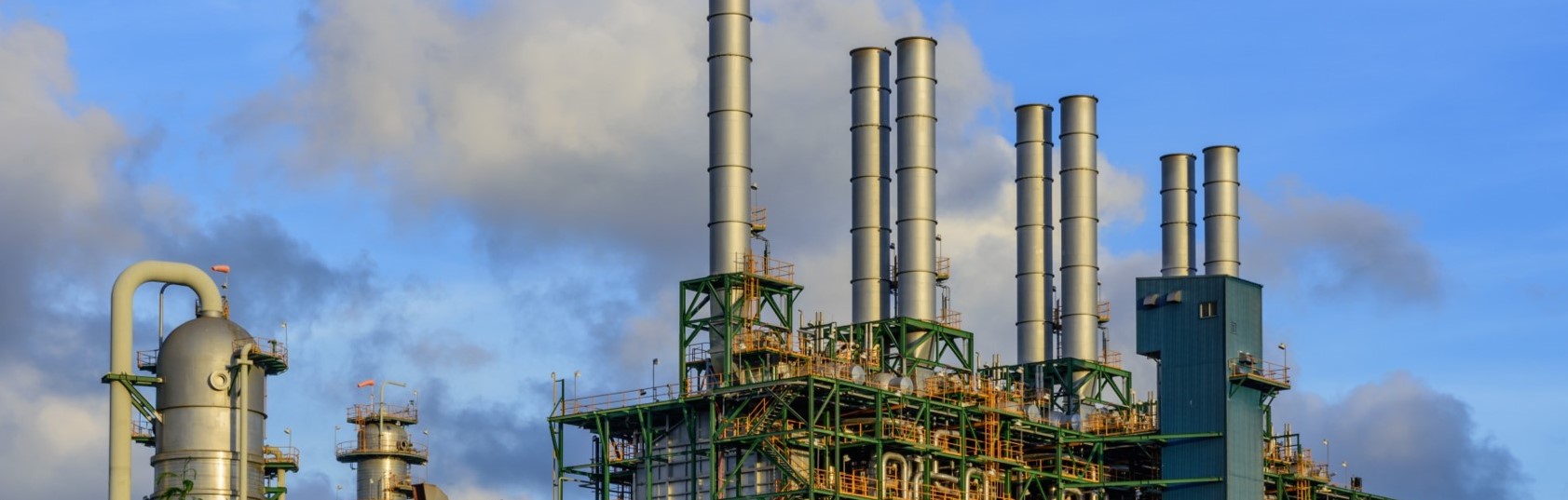
La formation interne de coke sur les réacteurs tubulaires de vapocraquage des unités d'éthylène a une influence majeure sur l'efficacité énergétique et la viabilité économique du procédé. Quand du coke se forme à l'intérieur des bobines de vapocraquage, cela entraîne une chute de pression plus importante, ce qui modifie la durée de fonctionnement et la sélectivité du produit de l'unité. En raison de la formation de coke, la température du métal du tube (TMT) augmente avec le temps, ce qui nécessite éventuellement la mise hors service du four pour le « décokage », ce qui entraîne une perte de production et une augmentation de la consommation énergétique et des coûts de maintenance.
De nombreux efforts ont été déployés ces dernières années pour développer des technologies permettant de réduire la formation de coke. Veolia a développé un revêtement catalytique breveté et novateur, appelé YieldUp, présentant une structure chimique unique capable de convertir le coke en oxydes de carbone au contact.
Le revêtement innovant YieldUp a été appliqué sur les nouveaux tubes de four qui seront installés dans un vapocraqueur d'éthylène européen de 30 T/h, qui utilisait différents types de charges d'alimentation (par exemple, naphte, GPL et butane), afin de déterminer son efficacité et sa durabilité. Les tubes revêtus ont été utilisés pendant une période de 36 mois pour déterminer s'ils permettaient de réduire la fréquence de décokage, qui était auparavant effectuée tous les 40 jours avec des tubes non revêtus.
Figure 1 : Tube de four avec revêtement YieldUp
YieldUp est un revêtement catalytique breveté mis au point par notre centre de recherche et développement.
Le revêtement passive les sites catalytiquement actifs de l'alliage du réacteur, réduisant ainsi l'accumulation de dépôts de coke catalytique. Il entraîne la conversion du coke déposé en CO2 et en hydrogène par gazéification, en réagissant avec de la vapeur à haute température.
Les nouvelles bobines installées dans le craqueur d'éthylène européen ont été recouvertes d'une couche de 25 μm de YieldUp, qui a ensuite été frittée sur la surface interne de la bobine. Les bobines ont ensuite été assemblées, soudées et installées dans le vapocraqueur.
Tout en fonctionnant avec les tubes nouvellement revêtus, le four a traité diverses charges d'alimentation. Ceci a permis de surveiller la formation de dépôts de coke se produisant dans diverses conditions de fonctionnement.
Résultat
L'indicateur clé de l'efficacité et de la performance du revêtement est le profil de la température du métal du tube (TMT) pendant le fonctionnement (Figure 2).
Figure 2 : Surveillance de la TMT du four avec des tubes revêtus
La TMT initiale au cours du redémarrage, après décokage, était systématiquement inférieure de 10 à 20 °C (18 à 36 °F). Comme prévu, la courbe de la TMT pendant toute la durée de fonctionnement était plus plate que pour un four non revêtu, ce qui a entraîné une prolongation de la durée de fonctionnement du four jusqu'à ce que la TMT maximale de 1120 °C (2250 °F) soit atteinte.
La preuve de l'efficacité de YieldUp peut être observée après chaque cycle de décokéfaction, avec un pic de CO2, indiquant la gazéification du coke catalytique et la réduction de la formation de dépôts dans les tubes.
Des analyses métallurgiques ont également été réalisées sur les tubes traités après 9 mois de fonctionnement et de multiples cycles de décokage, confirmant la présence du revêtement, et donc sa durabilité après de multiples passages.
Au cours des 36 mois de fonctionnement avec les tubes revêtus de YieldUp, la fréquence de décokage du four a été réduite de moitié, ce qui a permis de doubler les durées de fonctionnement, qui sont passées de moins de 40 jours à une moyenne de presque 80 jours (figure 3).
Figure 3 : Délai entre deux décokages d'un four européen
Les économies de combustible associées à l'augmentation de l'efficacité du transfert de chaleur et à la réduction de la fréquence de décokage ont été estimées à ~3 %, soit une économie d'environ 500 000 € par an et une élimination de l'émission de ~3000 T/an de CO2. La réduction de la fréquence de décokage permet également d'augmenter le temps de fonctionnement, ce qui accroît la productivité de l'usine d'environ 3 %. On s'attend également à ce que la durée de vie de la bobine soit prolongée en raison de la diminution du fluage et de la carburation, ce qui représente des gains opérationnels importants.