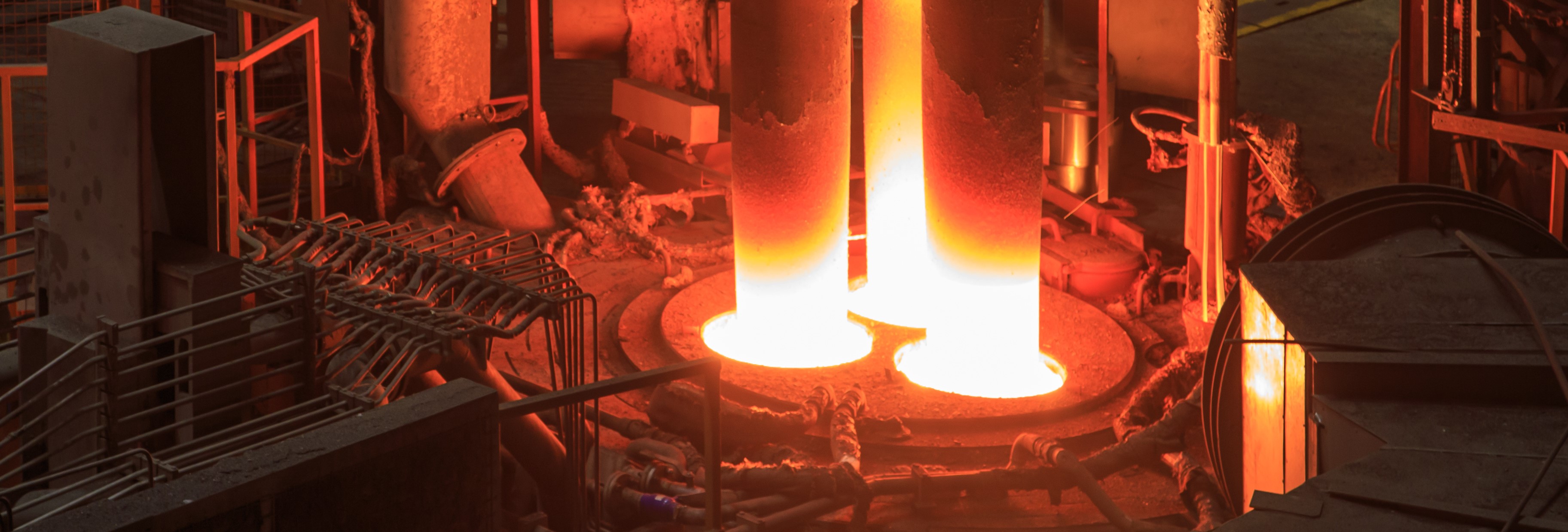
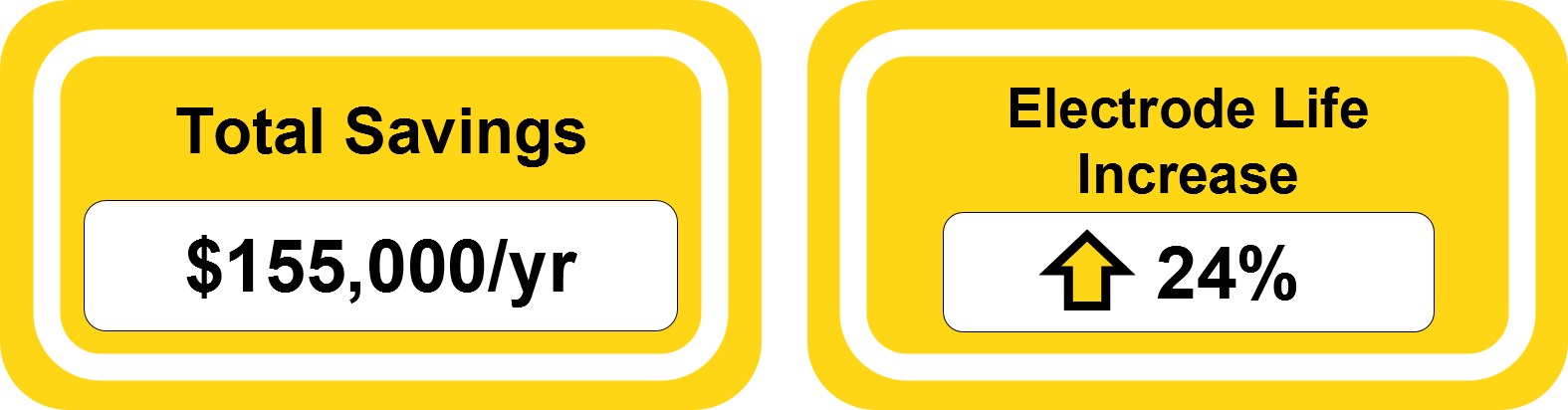
Les électrodes en graphite sont utilisées pour la fusion de l'acier dans le four à arc électrique de la plupart des ateliers de fusion des petites aciéries. Les électrodes sont un élément essentiel du processus de fabrication de l'acier, car elles transfèrent de grandes quantités de courant électrique et le convertissent en la chaleur qui est utilisée pour faire fondre la ferraille. Les électrodes sont consommées pendant le processus de fusion, car elles produisent un arc qui génère de la chaleur. Un mauvais refroidissement des électrodes entraîne une usure excessive et réduit leur durée de vie.
Une aciérie nord-américaine enregistrait un taux d'utilisation élevé des électrodes de phase 1, ce qui augmentait les coûts d'exploitation. Le défaut n'étant lié qu'à l'une des électrodes, l'usine a demandé à Veolia d'améliorer la supervision du flux de refroidissement des électrodes. Il a été suggéré de suivre les données dans le système de gestion des données de Veolia InSight*, système de gestion des données en nuage, qui était déjà utilisé pour d'autres usages dans l'aciérie. Le client a estimé qu'une meilleure maîtrise de la distribution de l'eau de refroidissement pourrait contribuer à atténuer le problème et à réduire les coûts de production.
Avant de proposer un quelconque traitement chimique, Veolia a procédé à une étude avec les ingénieurs de l'aciérie pour évaluer le contrôle du débit d'eau de refroidissement vers chaque électrode. Chaque électrode est dotée d'anneaux de pulvérisation avec de très petites ouvertures qui distribuent l'eau de refroidissement sur la surface de l'électrode de manière à assurer une couverture correcte de l'eau de refroidissement et une efficacité optimale du transfert de chaleur. Le mode de pulvérisation nécessite une quantité d'eau précise, étudiée pour minimiser l'oxydation des parois latérales et l'usure de des électrodes.
Les débits vers chaque phase des électrodes ont été téléchargés dans InSight et les modèles de débits ont été contrôlés en fonction de plusieurs chaleurs. Cela a permis de déterminer que la valeur de consigne pour l'électrode de phase 1 n'était pas respectée, car elle était 0,5-1,0 gal/min inférieure à la valeur cible, ou 15 % trop basse (figure 1).
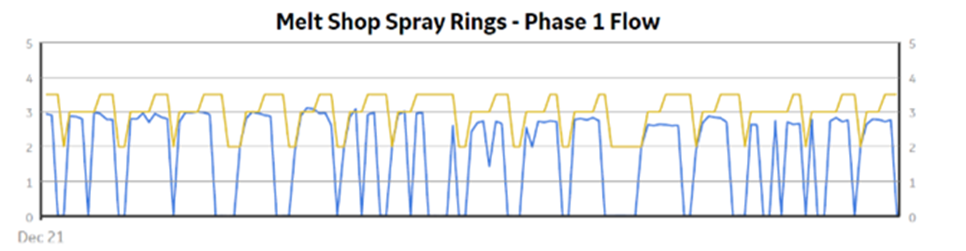
Figure 1 : le débit de la phase 1 (bleu) n'atteint pas la valeur de consigne (jaune)
Afin de confirmer que le débit de la phase 1 était effectivement inférieur à sa valeur de consigne, les signaux de débits des phases 1 et 2 ont été intervertis. Les données analysées à partir du système de gestion de données InSight de Veolia, basé sur le nuage, ont montré qu'une limitation du débit sur la canalisation d'eau de refroidissement était à l'origine du manque d'eau. Le client a donc procédé à des recherches supplémentaires sur la tuyauterie et a découvert que l'une des conduites avait été endommagée, réduisant ainsi le débit vers la phase 1. Cette situation a été corrigée et les débits ont été rétablis.
Résultat
Une fois que le débit de la ligne de refroidissement de la phase 1 a été rétabli, le débit de refroidissement a atteint la valeur de consigne (Figure 2). Ces conditions de débit appropriées ont considérablement augmenté la durée de vie des électrodes, d'environ 24 %.
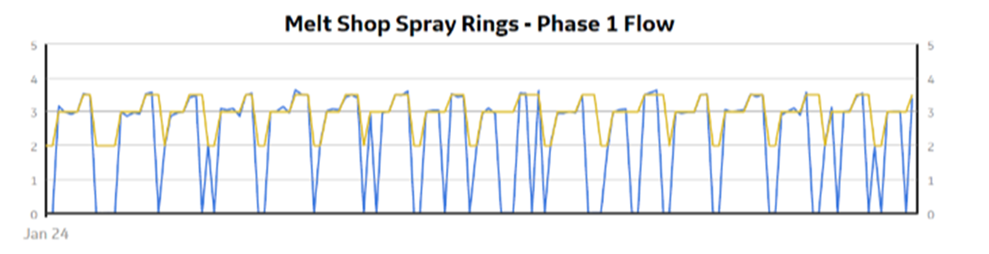
Figure 2 : Débit de la phase 1 (bleu) atteignant la valeur de consigne (jaune) lors de la découverte du problème de pincement de la canalisation
à l'aide des données de débit et de l'analyse InSight basée sur la gestion des données en nuage
Les données obtenues au cours de cette période d'essai témoignent d'un changement progressif dans le nombre de chauffes supportées par les électrodes de la phase 1 : de 13 chauffes à 17 chauffes par électrode. Cette réduction de la corrosion des électrodes grâce à l'optimisation du débit de refroidissement a permis à l'aciérie d'économiser environ 155 000 dollars par an.
Outre le problème de la consommation d'électrodes, il est essentiel d'éviter une oxydation inégale des parois latérales pour assurer une bonne transmission de l'arc au bain d'acier. Par conséquent, la garantie d'un débit d'eau de refroidissement adéquat par le biais d'une surveillance constante peut contribuer à maintenir la productivité, la qualité et la fiabilité du processus sans nécessairement nécessiter des traitements chimiques supplémentaires.
Découvrez-en plus sur nos solutions pour l'industrie sidérurgique