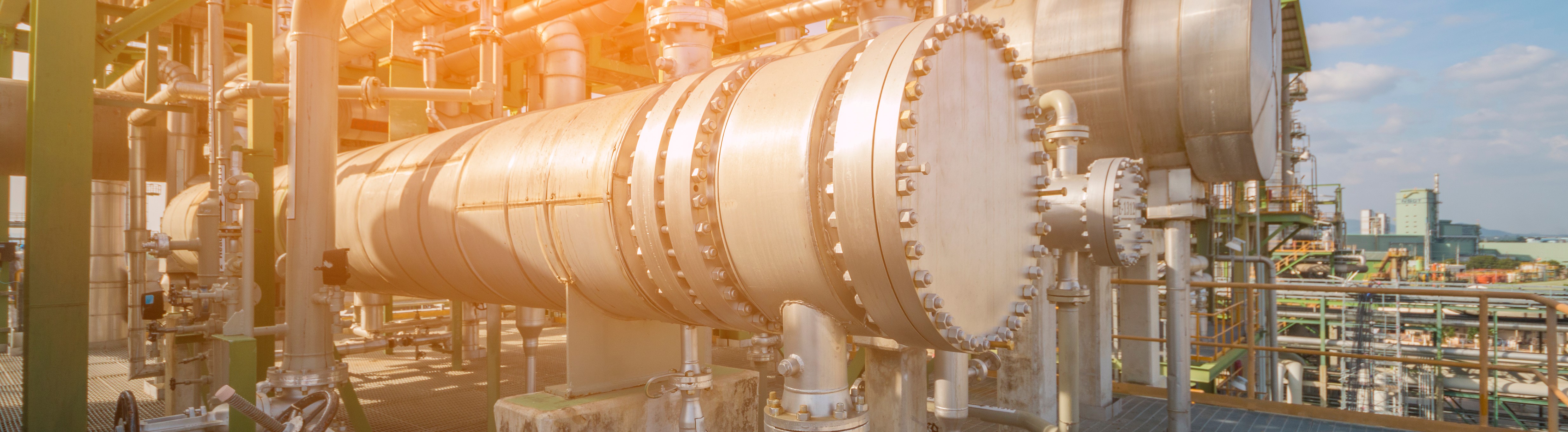
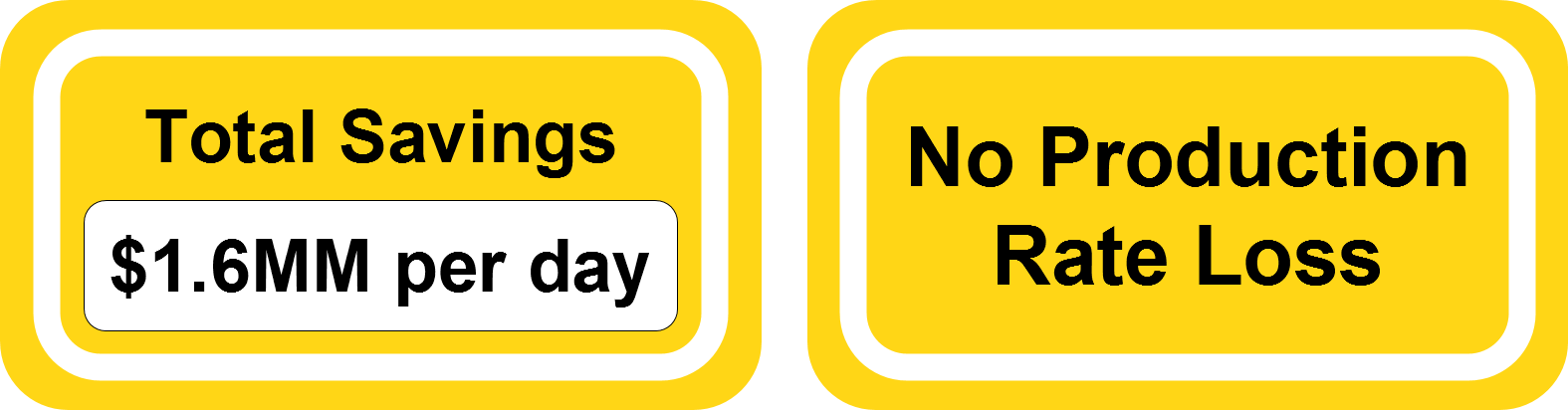
Une usine canadienne de valorisation du pétrole présentait un risque de perte de capacité de traitement de son eau acide sur l'ensemble du site en raison de la formation de mousse dans la partie supérieure de la tour du concentrateur. La formation de mousse varie considérablement, souvent en raison de la contamination de l'eau acide de l'unité de cokéfaction en amont, et peut entraîner des difficultés d'exploitation.
En l'absence de solution de traitement lorsque ces événements survenaient, la seule option était de réduire de manière significative la charge de l'unité de cokéfaction en amont. Par le passé, un seul épisode de moussage a impliqué une baisse de 42 % du taux de traitement de l'unité de cokéfaction en amont, réduisant ainsi la production de 50 KBBL (figure 2). Cet événement a duré 30 jours et a coûté à l'usine 48 millions de dollars, soit 1,6 million de dollars par jour.
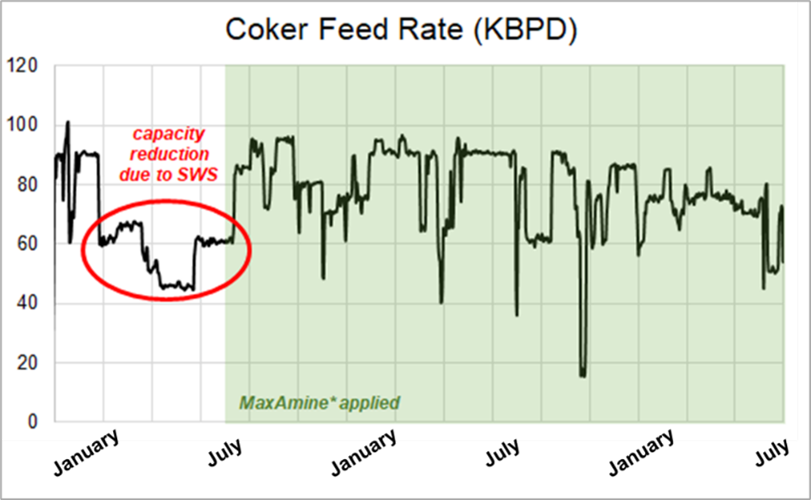
Figure 1. Le débit d'alimentation de l'unité de cokéfaction avec une capacité nominale de 95 KBPD a été réduit de 42 % en raison de la formation de mousse.
La tour de concentration d'eau acide a pour but d'extraire l'ammoniac et le sulfure d'hydrogène (H2S) des flux d'eau acide générés sur l'ensemble du site de l'unité de valorisation. La tour de concentration produit de l'eau acide épurée qui peut être réutilisée dans le processus, ainsi que des effluents liquides concentrés.
Les hydrocarbures aromatiques, tels que le naphta, peuvent être une source majeure de contamination dans le débit d'entrée du concentrateur d'eau acide, provoquant la formation de mousse à l'intérieur de la tour. La mousse agit comme un " support " physique, causant un débordement de liquide dans l'accumulateur de tête du concentrateur, ce qui limite le taux global de traitement de la charge des unités de cokéfaction.
Sur ce site de valorisation, l'eau acide provenant du processus de cokéfaction en amont s'est avérée régulièrement contaminée par des hydrocarbures aromatiques, entraînant des épisodes de moussage importants et des débordements de liquides excédentaires. L'équipe d'ingénieurs de l'usine de valorisation a travaillé en étroite collaboration avec Veolia pour identifier le problème de la formation de mousse et trouver une solution qui réduirait le risque d'entraînement de liquide et la réduction du débit de l'unité de cokéfaction.
Max-Amine, un produit chimique antimousse à base d'hydrocarbures, a été retenu comme la meilleure solution, car il s'agit d'une solution chimique en ligne, facile à utiliser, destinée à atténuer les phénomènes de moussage variables au niveau du concentrateur d'eau acide sans réduire le taux de traitement de l'unité de cokéfaction.
Résultat
L'application d'un antimousse a permis de réduire le phénomène de moussage dans la tour de concentration d'eau acide et de donner à l'unité de valorisation la souplesse nécessaire pour fonctionner à la capacité maximale de traitement de l'unité de cokéfaction.
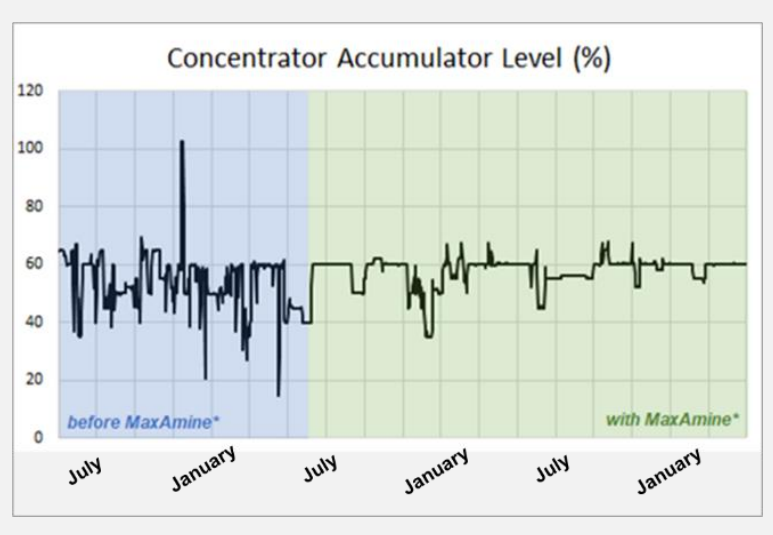
Figure 2. Niveau de l'accumulateur de tête du concentrateur avant et après injection de Max-Amine.
Veolia a conservé un excellent partenariat avec l'équipe d'exploitation de l'usine de valorisation, car l'application de Max-Amine a permis de stabiliser la teneur en eau acide et d'éviter la réduction du taux de traitement de l'une des unités de cokéfaction. Cela a permis d'éviter une nouvelle panne de l'unité de strippage de l'eau acide, semblable à la précédente, qui avait coûté 48 millions de dollars sur 30 jours, soit 1,6 million de dollars par jour.
De façon générale, l'application de l'antimousse Max-Amine a permis la suppression de tout temps d'arrêt de la production et de la nécessité de réacheminer les volumes des réservoirs d'eau acide. Les économies réalisées par le client grâce à l'application de l'antimousse ont été estimées à 1,6 million par jour en pertes de production évitées.